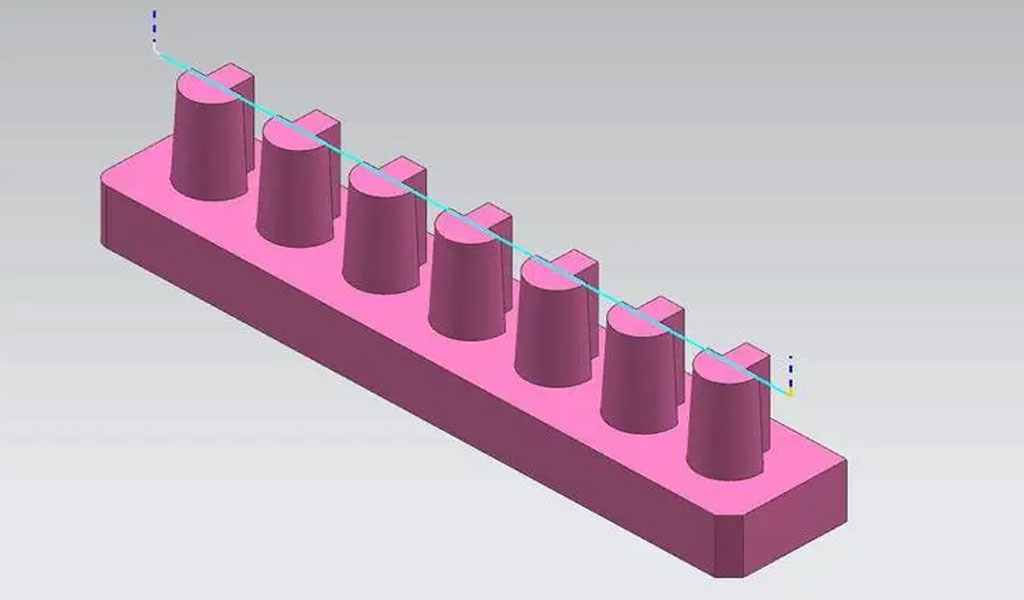
הזרקה היא אבן יסוד בייצור חלקי פלסטיק, וממלאת תפקיד מרכזי בתעשיות מגוונות. מציוד רפואי ועד לחללי רכב, מארזים אלקטרוניים ועד כלי בית יומיומיים ומעבר לכך, אין להכחיש את נוכחותם של חלקים יצוקים בהזרקה.
התהליך כולל המסת פלסטיק גולמי במכונת הזרקה, עיצובו בתוך תבנית ומתן לו להתקרר ולהתמצק, תוך ייצור רכיבים מעוצבים בצורה מורכבת.
המורכבות של עיצוב חלקי פלסטיק דורשת תשומת לב קפדנית לגורמים שונים, כולל דרישות פונקציונליות, בחירת חומרים ושיקולים מבניים. בין מרכיבי המפתח החיוניים לתהליך עיצוב זה הם עובי דופן, טיוטה, טקסטורות, צלעות, ובעיקר, בוסים.
המשמשים כנקודות חיבור והרכבה, בוסים הם בדרך כלל יציאות גליליות עם חורים הממוקמים אסטרטגית עבור ברגים או תוספות הברגה. הבטחת העיצוב האפקטיבי שלהם הוא בעל חשיבות עליונה, ודורש רדיוסי בסיס נדיבים לחוזק וטיוטה בשפע להסרה חלקה של חלקים מהתבנית.
בלוג זה מתעמק בקווים המנחים הבסיסיים לעיצוב בוס בחלקים יצוקים בהזרקה, במטרה לשפר את יכולת העיצוב, להאריך את חיי התבנית, להגדיל את אורך החיים התפעולי של החלקים ולהפחית את עלויות הייצור.
עיצוב בוס: סקירה קצרה
בעיצוב חלקים יצוקים מפלסטיק, אלמנט חיוני הדורש תשומת לב הוא הרעיון של עיצוב בוס. מה בדיוק מהווה בוס בתוך חלקים יצוקים? בבסיסו, בוס הוא תכונה מבנית – הקרנה גלילית הכוללת חורים ממוקמים אסטרטגית בתוך רכיבים יצוקים.
התפקיד העיקרי של הבוסים כולל מתן נקודות חיבור לברגים, מחברים או חומרה חיונית אחרת להרכבה. תכונות אלו ממלאות תפקיד מרכזי בהקלת תהליכי הרכבה חלקים תוך הבטחת השלמות המבנית של המוצר הסופי.
הבנה ושליטה בעיצוב הבוס היא הכרחית למיטוב הפונקציונליות ויכולת הייצור של חלקים יצוקים מפלסטיק.
אלמנטים עיצוביים של בוס
עיצוב בוס אפקטיבי הוא חיוני לשלמות המבנית של חלקים יצוקים. כדי להשיג חוזק אופטימלי מבלי להתפשר על העיצוב הכולל, מספר אלמנטים מרכזיים דורשים התייחסות מדוקדקת:
יחס עובי
עובי הדופן של בוסים לא יעלה על 60 אחוז מעובי הדופן הראשי של החלק. יצירת איזון זה חיונית כדי להבטיח את כוחו של הבוס מבלי לפגוע בשלמות המבנית הכוללת של החלק המעוצב.
יחס רדיוס בסיס
יציבות ומניעת עיוות במהלך הייצור מסתמכים במידה רבה על יחס רדיוס הבסיס. רדיוס הבסיס צריך להיות לפחות 25 אחוז מעובי הדופן הראשית, כדי לספק בסיס חזק. זה מתאים לקוטר בסיס של לפחות 50 אחוז, מה שתורם לחוסן הכללי של הבוס.
חיבור לקירות סמוכים
בוסים תמיד צריכים להיות מחוברים לקירות סמוכים באמצעות צלעות או שקעים. חיבור אסטרטגי זה עוזר להימנע מיצירת קטעים עבים, וממזער את הסיכון לעיוות במהלך תהליך הייצור. עיצוב מתחשב מבטיח שילוב חלק של הבוסים במבנה החלק הכולל.
יחס פילה בבסיס
כנקודת חיבור בין שני משטחים, בסיס הבוסים דורש יחס פילה לתוספת חוזק. אמצעי מניעה זה מגן מפני מתחים פוטנציאליים הנגרמים על ידי החדרת ברגים או חומרה אחרת, מבטיח עמידות וממזער את הסיכון לשבר.
שילוב יחס פילה הוא שלב קריטי בשיפור אורך החיים והאמינות של הבוס בתוך החלק היצוק.
10 הנחיות קריטיות לעיצוב בוס עבור חלקי פלסטיק יצוקים
רדיוס מינימלי בבסיס הבוס
יישום פילה עם רדיוס מינימלי ספציפי בבסיס של בוס הוא הכרחי כדי להפחית את ריכוז הלחץ. רדיוס זה ממוקם באופן אסטרטגי במקום שבו הבוס מצטלב עם הקיר הנומינלי, ובכך מפחית ביעילות את הלחץ ומשפר את השלמות המבנית הכוללת.
בעוד שהרדיוס מספק חוזק, יש לשלוט בו בקפידה כדי להימנע מקטעים עבים, לאזן בין תמיכה מבנית ויכולת ייצור. הטווח המומלץ עבור רדיוס בסיס זה הוא פי 0.25-0.5 מעובי הדופן הנומינלי, מה שמבטיח ביצועים מיטביים במהלך תהליך היציקה.
מרווח בין בוסים
ההצבה האסטרטגית של הבוסים חיונית למניעת יצירת אזורים דקים המציבים אתגרים בתהליך הקירור. שמירה על מרווח מתאים בין בוסים, באופן אידיאלי לפחות פי 2 מעובי הדופן הנומינלי, חיונית לקירור יעיל ולשיפור האיכות.
קרבה בין הבוסים עלולה להוביל לקשיים בקירור, להשפיע על הפרודוקטיביות ועל חיי העובש. מרווח נכון הוא המפתח להבטחת קירור אחיד ולשיפור אורך החיים של התבנית.
רדיוס בבסיס Hole In Boss
הכנסת רדיוס בבסיס החור בבוס משרתת מספר מטרות, כולל הימנעות מפינות חדות וריכוז מתח. תכונת עיצוב זו מסייעת בתהליך היציקה ותורמת להפחתת מתח, ומבטיחה את אורך החיים של החלק היצוק.
הרדיוס המומלץ בבסיס החור בבוסה נופל בטווח של 0.25 עד פי 0.5 מעובי הדופן הנומינלי, מה שמייצר איזון בין יכולת ייצור והפחתת מתח.
מינימום דראפט עבור Boss OD
הבטחת פליטה קלה מהתבנית דורשת טיוטה מתאימה על הקוטר החיצוני של הבוס (OD). טיוטה זו, בדרך כלל גדולה מ-0.5 מעלות או שווה ל-0.5 מעלות, מקלה על תהליך פירוק חלק.
טיוטה נאותה על פני השטח החיצוניים של הבוס לא רק מייעלת את הייצור אלא גם תורמת ליעילות של תהליך ההזרקה, וממזערת את אתגרי הייצור.
מינימום דראפט עבור Boss ID
שיקולי עיצוב מחייבים לעתים קרובות הפחתה מינימלית בקוטר הפנימי של הבוס (ID) לצורך התקשרות נכונה עם מחברים.
מומלצת טיוטה גדולה מ-0.25 מעלות או שווה ל-0.25 מעלות על הקירות הפנימיים של הבוס, כדי להבטיח פירוק חלק ויצירת התאמה בטוחה של מחברים. טיוטה זו על המזהה תורמת הן ליכולת הייצור והן לפונקציונליות של החלק המעוצב הסופי.
יחס גובה ל-OD בוס
שמירה על האיזון הנכון בגובה הבוס ביחס לקוטר החיצוני (OD) חיונית למניעת מסת חומר לא רצוי וחתכים עבים בבסיס.
עם גובה מומלץ של פחות מפי שלושה מהקוטר החיצוני, קו מנחה זה תומך בקירור יעיל, זמן מחזור מופחת ודיוק ממדי עבור חורים עם ליבה. יחס נכון בין גובה ל-OD חיוני לביצועים מיטביים של החלק.
רדיוס מינימלי בקצה הבוס
כדי לסבול עומסים משתנים במהלך תנאי השירות, חיוני לספק פילה עם רדיוס מינימלי ספציפי בקצה הבוס. תכונת עיצוב זו מפחיתה ביעילות את ריכוז המתח ומשפרת את העמידות והחיים הכוללים של החלק המעוצב.
הרדיוס המינימלי המומלץ בקצה תורם לחוסן הכללי של הבוס בתרחישי טעינה שונים.
צ'אמפר בצמרת הבוס
שילוב של שיפוע בחלק העליון של בוס הוא הובלה מועילה עבור מחברים במהלך תהליך ההרכבה. תכונת עיצוב זו מבטיחה חיבור ויישור חלקים במהלך ההרכבה, ומייעלת את תהליך הייצור.
השיפוע בחלק העליון של הבוס תורם לקלות ההרכבה ולאיכות הכללית של החלק המעוצב הסופי.
עובי קיר של בוס
שמירה על עובי דופן אידיאלי לבוסים, בערך 60 אחוז מהקיר הנומינלי, היא קריטית כדי למנוע בעיות כמו חללים, סימני כיור וזמני מחזור ממושכים.
למרות שחרוג מעובי זה עלול להוביל לאתגרים בייצור, התאמת עובי הדופן עשויה להיחשב עבור בוסים באזורים שאינם נראים לעין, מה שמאפשר לחצים מוגברים המוטלים על ידי ברגים עם הקשה עצמית. יצירת האיזון הנכון בעובי הדופן חיונית לביצועים מיטביים של החלק.
בוס עצמאי
יישום ליבה עבור בוסים וחלקים עבים אחרים מומלץ כדי להבטיח זרימת חומר אחידה וחלוקת עומסים. חיבור הבוס לדופן משפר את הקשיחות ואת זרימת החומר, תורם לשלמות המבנית הכוללת של החלק היצוק.
שיקול עיצובי זה חיוני להשגת ביצועי חלק ויכולת ייצור משופרים.
האתגרים והפתרונות בעיצוב בוס
עיצוב בוס לא נכון מציב אתגרים שיכולים להשפיע באופן משמעותי על האסתטיקה והפונקציונליות של חלקים יצוקים. מהם האתגרים הללו? איך אפשר לפתור אותם? בואו לחקור למטה.
גרימת סימני כיור ועיוות
אתגר
אחד האתגרים העיקריים בעיצוב בוס הוא הפוטנציאל לסימני כיור ועיוותים. כאשר הבוסים מעוצבים בצורה לא מספקת – עבים מדי או חסרי חיזוק מתאים – הם מתקררים בקצב שונה מהאזורים שמסביב.
פער טמפרטורה זה יכול להוביל לסימני שקיעה מכוערים, ליצור שקעים על פני השטח והתעוותות, ולגרום לסטייה של החלק מצורתו המיועדת.
פִּתָרוֹן
התמודדות עם אתגר זה כרוכה באופטימיזציה של עובי הדופן של בוסים ושילוב צלעות חיזוק. עובי דופן מתאים מבטיח קירור אחיד, וממזער את הסיכון לסימני שקיעה ועיוות. צלעות חיזוק חיוניות בחלוקת הלחץ באופן שווה על פני הבוס, מניעת דפורמציה מקומית ושיפור שלמות החלק הכוללת.
השפעה על זמן קירור וזמן מחזור
אתגר
בוסים משפיעים ישירות על זמני הקירור והמחזור במהלך תהליך הדפוס. במקרים בהם הבוסים עבים מדי או מעוצבים בצורה גרועה, הם עלולים ללכוד חום, וכתוצאה מכך זמני קירור וזמני מחזור ממושכים.
זה לא רק מאט את תהליך הייצור אלא גם מוביל להגדלת עלויות הייצור.
פִּתָרוֹן
הפחתת ההשפעה על זמני הקירור והמחזור כרוכה בהתאמות אסטרטגיות לתעלות הקירור בתוך התבנית. אופטימיזציה של עיצוב העובש הכולל, תוך תשומת לב מיוחדת למיקום הבוסים, יכולה למזער את ההשפעות השליליות על זמני הקירור והמחזור.
מבחר חומרים מוגבל ותאימות
אתגר
החומר שנבחר עבור חלקים יצוקים משפיע באופן משמעותי על עיצוב הבוס. בחירת חומר לא תואם עלולה להעמיד את הבוס ללחץ מוגזם, שעלול להוביל לסדקים או כישלון.
פִּתָרוֹן
ההתגברות על האתגר הזה סובבת סביב בחירת החומר המתאים לעיצוב הבוס. בחר בחומר עם החוזק, הקשיחות והעמידות הכימית הדרושים כדי להבטיח שהבוס יכול לעמוד בעומסים ובתנאי הסביבה.
בחירת חומר חיונית להשגת עיצובי בוס עמידים ואמינים בחלקים יצוקים.
סיכום
בוסים בחלקים יצוקים בהזרקה משמשים כמאפיינים מכריעים, הפועלים כעוגנים, תומכים ומסייעים להרכבה אמינה. רכיבים אלה ממלאים תפקיד מכריע בהבטחת השלמות המבנית והביצועים האופטימליים של המוצר הסופי.
הקפדה על הנחיות עיצוב בסיסיות היא הכרחית כדי לייצר חלקי פלסטיק עם בוסים חזקים, פונקציונליים ומושכים חזותית.
עבור אלה המחפשים חלקים יצוקים באיכות מעולה עם עיצוב בוס אמין, BE-CU מתגלה כבחירה האופטימלית. שירותי ההזרקה שלנו מגובים על ידי צוות מנוסה המחויב לעמוד בדרישות הספציפיות שלך. רוצים לדעת עוד? צרו קשר עוד היום!