ייצור רזה, המושרש בעקרונות שנקבעו על ידי יצרנית הרכב היפנית טויוטה, הוא גישה טרנספורמטיבית שמטרתה לצמצם בזבוז בפיתוח ובייצור מוצרים. מטרות הליבה – ביטול עומס יתר (Muri), חוסר עקביות (Mura) ובזבוז (Muda) – עומדות בבסיס מערכת Just-in-Time (JIT). JIT מאגד בתוכו את האתוס של ייצור רק "מה שצריך, מתי נחוץ, ובכמות הדרושה", ומטפח יעילות והפחתת שגיאות. בניגוד לתפיסות השגויות, ביטול הפסולת בייצור רזה אינו קשור לקיצוץ בכוח העבודה אלא במתן ערך בר-קיימא ללקוחות. זה משפר את זמני ההובלה, מגביר את איכות המוצר ומצמצם את עלויות התפעול, ומבטיח תחרותיות לטווח ארוך. ככל שהייצור מתפתח, עקרונות רזה משמשים כמצפן, מניעים שיפור מתמיד, מייעל תהליכים ואימוץ טכנולוגיות חדשניות כדי לספק מוצרים איכותיים במהירות ובמחיר יעיל.
כיצד פועל ייצור רזה
באמצעות איתור ופינוי פסולת, ייצור רזה מבקש לשפר את האיכות, לקצר את זמני הייצור ולחסוך בהוצאות. ישנן שתי אסטרטגיות עיקריות: האסטרטגיה המסורתית ממוקדת פסולת ו-'Toyota Way', המעניקה עדיפות לאופטימיזציה של תהליכים על פני הפחתת פסולת. שיטת טויוטה אינה מכוונת ישירות לפסולת בודדת; במקום זאת, היא דורשת גישה מקיפה, כלל מערכתית המעודדת חשיבה רזה בכל חברה. זה הופך את המסגרות התפעוליות לפשוטות יותר כדי לסייע בהבנה ובניהול. חונכות 'Senpai ו-Kohai' (בכיר וג'וניור) כלולה גם היא בשיטה לטפח חשיבה רזה בכל ההיררכיה הארגונית.
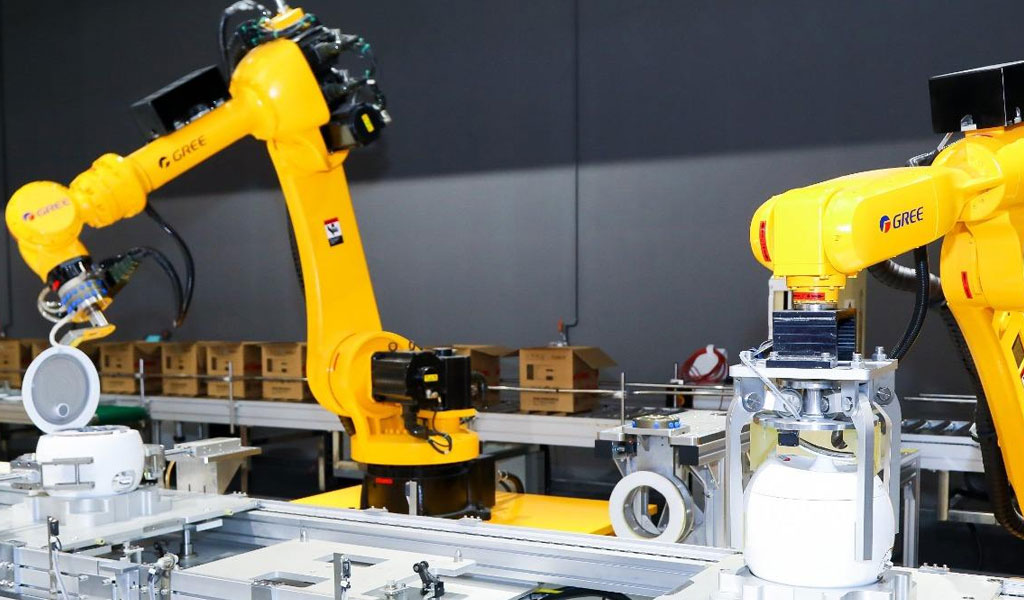
מושגי מפתח כמו אוטומציה, שיפור מתמיד, התאמה, פילוס עומס, ייצור או שירות ללא רבב בפעם הראשונה, זרימת ייצור ושליטה ויזואלית, עיבוד משיכה, חיבורי ספקים והפחתת פסולת משותפים לשתי הטכניקות למרות המתודולוגיות השונות שלהן. התהליכים מתייעל באמצעות אוטומציה, ושיפורים מובטחים על ידי שיפור מתמיד. התאמה לצרכים משתנים מתאפשרת בזכות גמישות, בעוד שצריכת המשאבים מוגברת באמצעות פילוס עומס. מתן עדיפות לאיכות ללא רבב מההתחלה מפחית שגיאות, בעוד שבקרה ויזואלית וזרימת ייצור משפרים את השקיפות התפעולית. עיבוד משיכה עוזר להתאים את התפוקה לביקוש האמיתי, וקשרי עבודה טובים עם ספקים מקדמים שיתוף פעולה. כך או כך, המטרה של ייצור רזה היא למקסם את הפרודוקטיביות והאיכות בכל החברה.
חמישה עקרונות של ייצור רזה
Lean Manufacturing מדגישה חמישה עקרונות מפתח למיטוב מערכות הייצור:
יצירת ערך ללקוח
ב-Lean Manufacturing, ההתמקדות העיקרית היא ביצירת ערך יעיל ללקוח. השלב הראשוני כולל זיהוי תכונות מוצר חיוניות באמצעות העדפות הלקוח. על ידי התאמת הייצור לצרכי הלקוח, הדגש הוא על ביטול רכיבים לא חיוניים, ייעול תהליכים להגדלת הערך, והבטחה שהמוצר הסופי יהדהד עם ציפיות הלקוח.
מיפוי זרם ערך
הגישה הרזה מגדירה את זרם הערך כרצף השלבים המוסיפים ערך ללקוח לאורך הייצור. הדמיה של תהליך זה באמצעות מפת זרם ערך מאפשרת למנהלים לאתר חוסר יעילות, למזער בזבוז ולזהות דרכים לשיפור. עזר חזותי זה מספק תובנות על מסע הייצור כולו, ומסייע באופטימיזציה של תהליך הייצור.
יצירת זרימה
Lean Manufacturing דוגלת בשיפור תהליכים מתמיד, תוך התייחסות לבעיות כגון פריסות מתקנים לא אופטימליות. שיפור זרימת זרם הערך כרוך בביטול צווארי בקבוק וחסמים הפוגעים ביעילות. תהליך יעיל מבטיח זרימת ייצור חלקה יותר, שיפור הפרודוקטיביות הכוללת והיענות לדרישות הלקוח.
יישום מערכת Pull
מערכת המשיכה, חלק בלתי נפרד מ-Lean Manufacturing, מכתיבה ייזום עבודה חדשה רק בתגובה לדרישת הלקוח. גישה זו מבטלת פעילויות בזבזניות כמו עודף אחסון מלאי ותחבורה מיותרת. על ידי התאמת הייצור לביקוש, מערכת המשיכה תומכת במודל ייצור בדיוק בזמן, הפחתת בזבוז והגברת היעילות.
שיפור מתמיד (Kaizen)
Kaizen, שם נרדף לשיפור מתמיד, כרוכה בביצוע שינויים מצטברים כדי לשפר תהליכים לאורך זמן. ב-Lean Manufacturing, Kaizen מאפשרת לעסקים לזהות ולטפל בבעיות באופן שיטתי, תוך מיקסום ערך הלקוח תוך מזעור בזבוז. באמצעות שיפורים קטנים ומתמשכים, ארגונים מטפחים תרבות של שיפור מתמשך ופתרון בעיות.
טויוטה, חלוצה בייצור רזה, משתמשת במתודולוגיית חונכות בשם Senpai ו-Kohai (בכיר וזוטר). גישה זו משרה חשיבה רזה בכל המבנה הארגוני, מטפחת מחויבות יסוד ליעילות ולהפחתת פסולת. לסיכום, העקרונות של Lean Manufacturing, המושרשים במרכזיות לקוחות ושיפור מתמיד, מציעים מסגרת לעסקים לייעל תפעול ולשפר את יעילות הייצור הכוללת.
סוגי פסולת בייצור רזה
ייצור רזה שם דגש חזק על חיתוך פסולת כדי להגדיל את הפרודוקטיביות ולספק לצרכנים ערך. השגת הבנה של שמונה קטגוריות הפסולת חיונית לייעול הפעילות ולשיפור ביצועי החברה הכוללים.
פגמים
פגמים גלויים ויקרים מובילים לפריטים שאינם עומדים בדרישות, דבר המעכב את האספקה ומעצבן את הלקוחות. עיבוד מחדש של מוצרים פגומים עולה כסף מכיוון שזה דורש זמן ומשאבים. צמצום הפסדים כספיים ושמירה על אושר הלקוחות תלויים בניהול ליקויים יעיל.
תְפוּקַת יֶתֶר
כאשר הייצור עולה על הביקוש הצרכני, נוצר מלאי נוסף, נוצרות עלויות אחסון ומתרחשת הידרדרות אפשרית של המוצר. ניתן לעקוב אחר זמן ההיצע, או הקצב שבו ההיצע עונה על הביקוש, כדי לעזור להתאים את ההיצע לביקוש האמיתי ולמנוע ייצור יתר והוצאות נלוות.
הַמתָנָה
כאשר צרכן או מוצר מוכנים לשלב הבא אך התהליך שאחריו אינו מוכן, מתרחשת המתנה. זה מוריד את שביעות רצון הצרכנים ועלול לגרום לעיכובים במספר תעשיות, כולל ייצור ושירותי בריאות. הפחתת פסולת המתנה דורשת מדידת זמן מדויקת ושינויים בתכנון התהליך.
כישרון לא מנוצל
מקור עיקרי לבזבוז כישרונות לא מנוצל הוא התעלמות מהיכולות והפוטנציאל של העובדים. יעילות כוח העבודה נפגעת על ידי עבודת צוות לא יעילה, הכשרה לא מספקת, פערי תקשורת ופעילויות אדמיניסטרטיביות חסרות טעם. השימוש הטוב ביותר בכישרון הצוות מובטח על ידי טיפול בבעיות אלו עם הכשרה מתאימה והשתתפות בשיפורי תהליכים.
הוֹבָלָה
פסולת הובלה היא תוצאה של תנועה של סחורות בין מקומות מבלי לתרום ערך למוצר הסופי. מערכות תחבורה לא יעילות מעלות הוצאות, משתמשות יותר באנרגיה, ואף עלולות לגרום נזק למוצר. כפי שהדגימה המתודולוגיה של טויוטה, הצבת מתקני ייצור קרובים לספקים מפחיתה את פסולת התחבורה ומגבירה את הפרודוקטיביות הכוללת.
מְלַאי
כאשר סחורה נשמרת בהישג יד בזמן שהם ממתינים למכירה, בזבוז מלאי קורה בדומה לייצור יתר. עלויות פיזיות קשורות למלאי רב מדי, וזה יכול לגרום לעלויות אחסון גבוהות יותר. על ידי הימנעות מייצור יתר ובזבוז מלאי, ייצור בדיוק בזמן עוזר לשמור על איזון בין רכש לביקוש הצרכני.
תְנוּעָה
בזבוז תנועה הוא הזזה מיותרת של כוח אדם, ציוד או חפצים אחרים שאינם בעלי ערך מוסף. זהו סימן לסטייה משיטות ייצור רזה. זמן הולך לאיבוד כתוצאה מאזורי עבודה מתוכננים בצורה גרועה ומיקום לא יעיל של חומרים או ציוד. ביטול בזבוז תנועה והגברת היעילות הכוללת הם שני יתרונות של אימוץ תפיסת הייצור הרזה של 5S.
עיבוד נוסף
עיבוד יתר, המכונה גם "עיבוד נוסף", הוא תוספת של עבודה שאינה חיונית ומביאה לבזבוז זמן, חומרים ובלאי ציוד. כתוצאה מכך, משאבים מופנים מעבודות שמביאות ערך, מה שמפחית את יעילות התהליך באופן כללי. פישוט תהליכים ותשומת לב לפרטים מפחיתים עיבוד מיותר ומגדילים את התפוקה באופן כללי.
יתרונות וחסרונות של ייצור רזה
יתרונות
חוסך כסף וזמן: היתרון הבולט ביותר של ייצור רזה הוא הפחתת עלויות. ללא קשר לגודל או תפוקה, ארגונים עשויים להרוויח מתהליכים יעילים יותר, הקצאת משאבים, ייצור ואחסון. בנוסף לאפשר זמני אספקה קצרים יותר ואספקת מוצרים מהירה יותר ללקוחות, אמצעים לחיסכון בזמן עשויים גם להביא לחיסכון בעלויות על ידי יצירת צוות יעיל יותר.
שביעות רצון משופרת של הלקוח יכולה להיות מושגת על ידי מתן מוצר או שירות טובים יותר ללקוח במחיר סביר. זה קריטי להצלחת הארגון שלך מכיוון שלקוחות מרוצים נוטים יותר להשתמש בסחורה או בשירותים שלך שוב או להפנות אחרים אליך.
ידידותית לסביבה: אתה עשוי לחסוך כסף על אנרגיה ובנזין על ידי צמצום פעולות בזבזניות ובזבוז פחות זמן ומשאבים. גם לזה וגם לפריסה של ציוד חסכוני יותר באנרגיה, שעשויה להביא גם לחיסכון בעלויות, יש יתרונות סביבתיים ברורים.
חסרונות
דאגות בטיחות ורווחת עובדים: מבקרים טוענים שייצור רזה עלול להזניח את בטיחות העובדים ורווחתם על ידי התמקדות יתר בהפחתת הפסולת. הלחץ האינטנסיבי להקפיד על נהלים יעילים עלול להתעלם מהאגרה של העובדים, שמזכיר טכניקות ניהול מיושנות מהמאה ה-19.
מכשול פוטנציאלי לפיתוח עתידי: ההתמקדות המובנית בהפחתת הפסולת עשויה להוביל את ההנהלה לקצץ באזורים הנחשבים לא חיוניים לאסטרטגיה הנוכחית. עם זאת, היבטים אלה עשויים להיות חיוניים למורשת ולפיתוח העתידי של החברה, ועלולים להפריע לצמיחה ארוכת טווח. ייצור רזה יכול ליצור דגש קוצר ראייה על ההווה על חשבון שיקולים עתידיים.
אתגרים בתקינה: מבקרים טוענים שייצור רזה, שהוא יותר גישה תרבותית מאשר שיטה נוקשה, חסר מודל ייצור מתוקנן. תפיסה זו עלולה לערער את האמינות של רזה כטכניקה חזקה ומוגדרת היטב.
הכלים הטובים ביותר לייצור רזה
ייצור רזה מסתמך על כלים שונים כדי לייעל תהליכים ולהגביר את היעילות. בין הכלים הטובים ביותר בגישה זו הם Kanban, Kaizen, Value Stream Mapping, 5S Management ו-Plan-Do-Check-Act (PDCA).
Kanban, בין אם בצורה דיגיטלית או פיזית, משמש אות לייצור באצווה קטנה, תוך אופטימיזציה של ניצול המשאבים. Kaizen, כלי לשיפור מתמיד, מעודד שינויים יומיים קטנים בכל רמות הארגון.
Value Stream Mapping הוא כלי רב-תכליתי שמנתח ומשפר את זרימת החומר והמידע לאורך כל מחזור חיי המוצר או השירות. בינתיים, ניהול 5S, הכולל מיון, קביעת סדר, ברק, סטנדרטיזציה ושמירה, הוא כלי פרודוקטיבי שמשפר את היעילות על ידי הפיכת חריגות לעין.
PDCA הוא כלי ניהול רזה בסיסי המקדם שיפור מתמיד. זה כרוך בתכנון יעדים ספציפיים, ביצוע המשימות הדרושות, הערכת תוצאות והתאמה לפי הצורך.
בנוסף לכלי ליבה אלו, מתודולוגיות שונות תורמות ליישום ניהול רזה. תרשימי בקרה מנטרים זרימות עבודה, לוחות Kanban מדגים תהליכים ו-5S מציעה מתודולוגיה לארגון מקום העבודה. טיפול מרובה תהליכים, הוכחת שגיאות (Poka-Yoke), ריכוז הזמנות דירוג, תזמון נקודה אחת, החלפת קוביות בדקה אחת (SMED) ותחזוקה פרודוקטיבית כוללת משכללים עוד יותר את תהליכי הייצור.
יתר על כן, תכנון מחדש של תא עבודה מייעל את הפריסה לשיפור זרימת העבודה. כלים אלו יוצרים ביחד מערכת ניהול רזה יעילה. הם כוללים היבטים כמו הדמיה של זרימת עבודה, ארגון מקום העבודה, מניעת שגיאות ושיפור מתמיד, התורמים לשיפור הפרודוקטיביות ולמצוינות תפעולית כוללת.
טיפים מעשיים לייצור רזה למכונות
אימוץ ייצור רזה בחנויות מכונות אינו רק אימוץ פרקטיקות ספציפיות; זוהי פילוסופיה דינמית הדורשת הבנה מעמיקה של העקרונות שלה. וומאק וג'ונס מדגישים את ההבחנה הקריטית בין אלה שרק מעתיקים פרקטיקות לבין אלה שתופסים את העקרונות הבסיסיים העומדים בבסיס המערכת הרזה כולה, תוך שימת דגש על הצלחתה של האחרונה.
כדי לטפח גישה רזה, ראה אותה כמסע מתמשך המחייב הערכה והתאמה מתמשכת. ארגז כלים רזה של שיטות יכול לפשט מערכות ניהול, אבל זכרו, רזה היא יותר פילוסופיה מאשר מערכת נוקשה של נהלים. להלן ארבעה שלבים מעשיים לעיצוב מערכת יעילה לניהול פרויקטים רזה המותאמת למכונות:
צור מערכת ייצור יעילה:
חלק את הפעולות שלך לחלקים פשוטים ומרוכבים לניטור קל יותר וביטול פסולת. פישוט תהליכים משפר את הנראות, מה שהופך את השיפורים לניתנים לניהול. שלב זה מתיישב עם המהות של חשיבה רזה – יעילות באמצעות פשטות.
המשך שיפור מתמיד:
העצים את הצוות בכל הרמות לחפש באופן פעיל דרכים טובות יותר לעשות דברים. עודד הערכה כנה של נהלים, איתור אזורים בשלים לשיפור. התאם את השיפורים הללו לתהליכים הספציפיים של חנות המכונות שלך ליעילות מירבית. ככל שהשיפורים מדויקים ורלוונטיים יותר, כך התוצאות משפיעות יותר.
יישם שיפורי עיצוב מתמשכים:
זיהוי שיפורים הוא רק ההתחלה; הם חייבים להיות משולבים בצורה חלקה בעיצובים, הנהלים והתהליכים שלך. בחר בשינויים מצטברים, הנתמכים על ידי מדדים מדידים. יישום מעשי הוא המפתח – ודא ששיפורים יתורגמו לשיפורים מוחשיים יומיומיים.
קניית צוות מאובטחת:
ההצלחה בשלושת השלבים הראשונים תלויה בהשגת תמיכת הצוות שלך. עקרונות ה-Lean מקיפים את העסק כולו, ומחייבים את הבנת ההנהלה בנושאים האמיתיים העומדים על הפרק. התנגדות עובדים יכולה לעכב את ההתקדמות, מה שהופך את זה חיוני לערב אותם במסע הרזה. קבע 'תוכנית רזה' לקבלת החלטות שיתופית, שבה צוותים תורמים משוב, וההנהלה מחליטה על שינויים. מאמן עובדים בכל הרמות להקניית הידע הדרוש ליישום רזה קולקטיבי ומוצלח.
סיכום
לסיכום, ייצור רזה – ששורשיו במערכת הייצור של טויוטה – נותן עדיפות לפינוי פסולת כדי להגדיל את הפרודוקטיביות והערך עבור הלקוחות. ערך, זרם ערך, זרימה, משיכה ושלמות – חמשת עמודי התווך של ייצור רזה – מאפשרים לחברות להפחית פסולת במגוון דרכים, כולל ייצור יתר ותקלות. הדגשת עיצוב פשוט ושיתוף פעולה עם הצוות עשויים למקסם את התוצאות, וכתוצאה מכך עלויות נמוכות יותר, איכות טובה יותר ויותר שביעות רצון לקוחות בשוק תחרותי, כולל שיטות כמו Kaizen ו- Kanban לקידום פיתוח מתמשך.